The process
All things come from Earth, and all things end by becoming Earth. Xenophanes
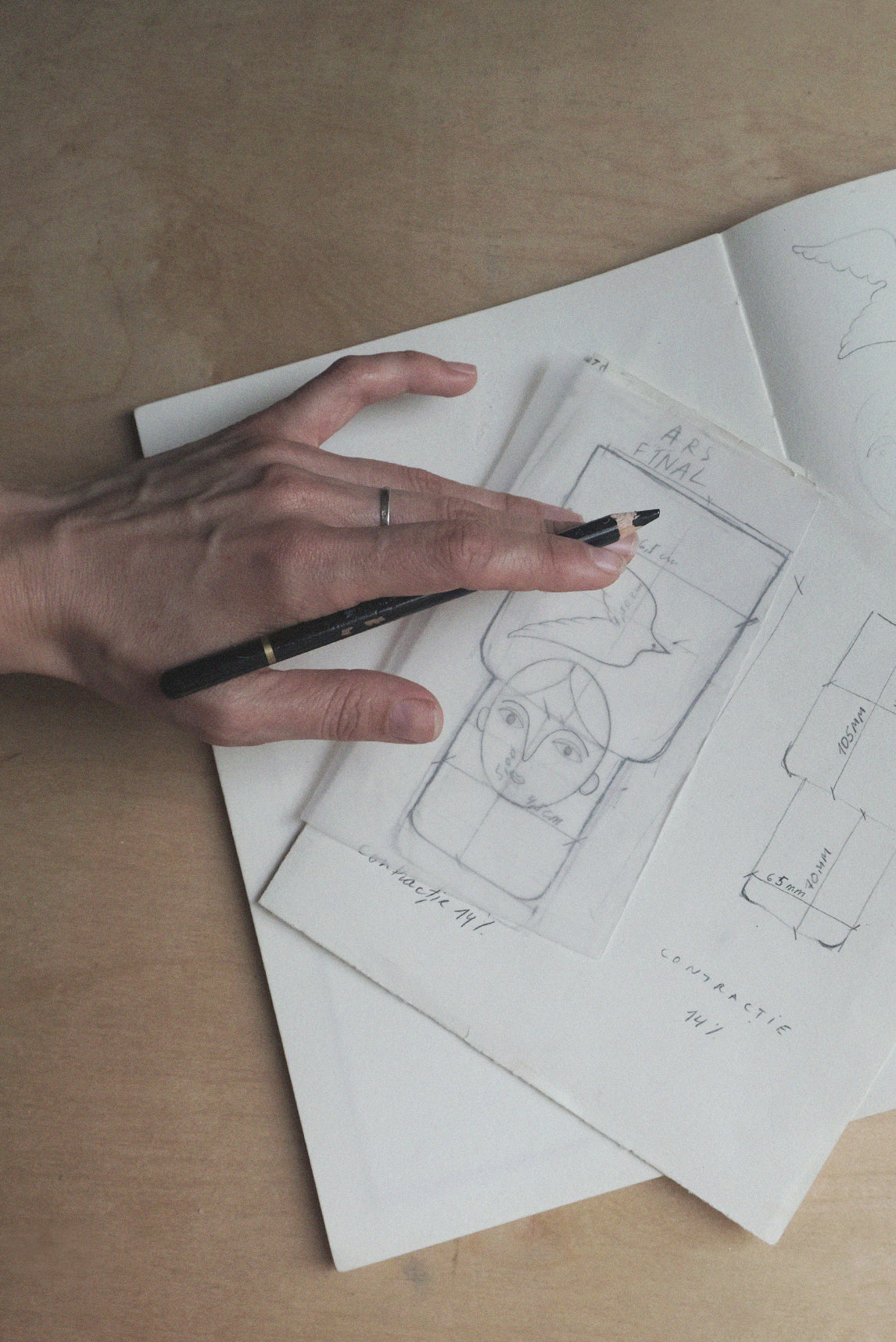
I. The pursuit of an idea
Inspired by timeless objects and images, inspired from poetry, music, literature, and storytelling, tradition and contemporaneity melt the influences in the pursuit of elegance and beauty. Every object starts with an idea, a dream that is put on paper.
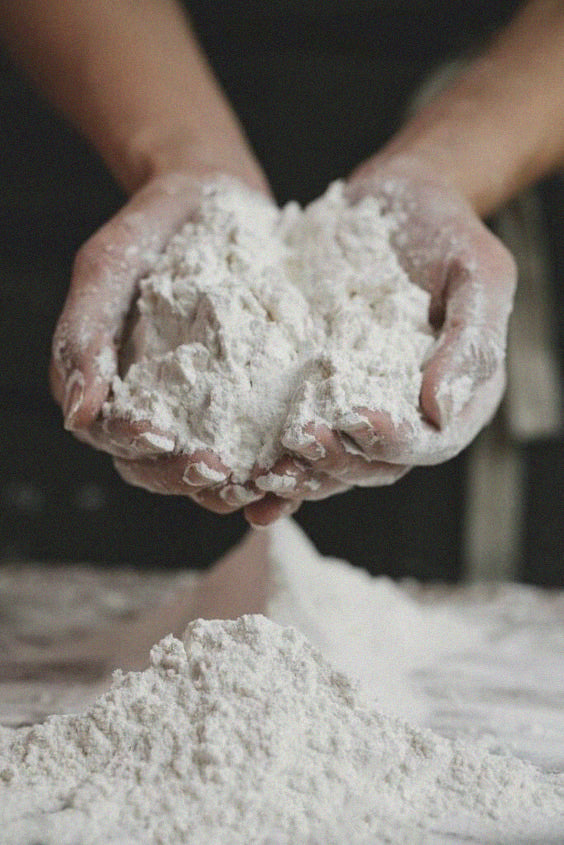
II. The materials
Everything starts from dust. The materials we start with are powders, powder of gypsum, for the molds, powder of porcelain for the paste, powder of cobalt oxide for the blue pigment, and powder of silicium for the glazing. It looks as a kitchen of witchcrafts, like magic.
Porcelain - 55% kaolin, 20% silica, 25% feldspar, 2% Bentone
Glazing - SiO2
Pigment - Co3O4
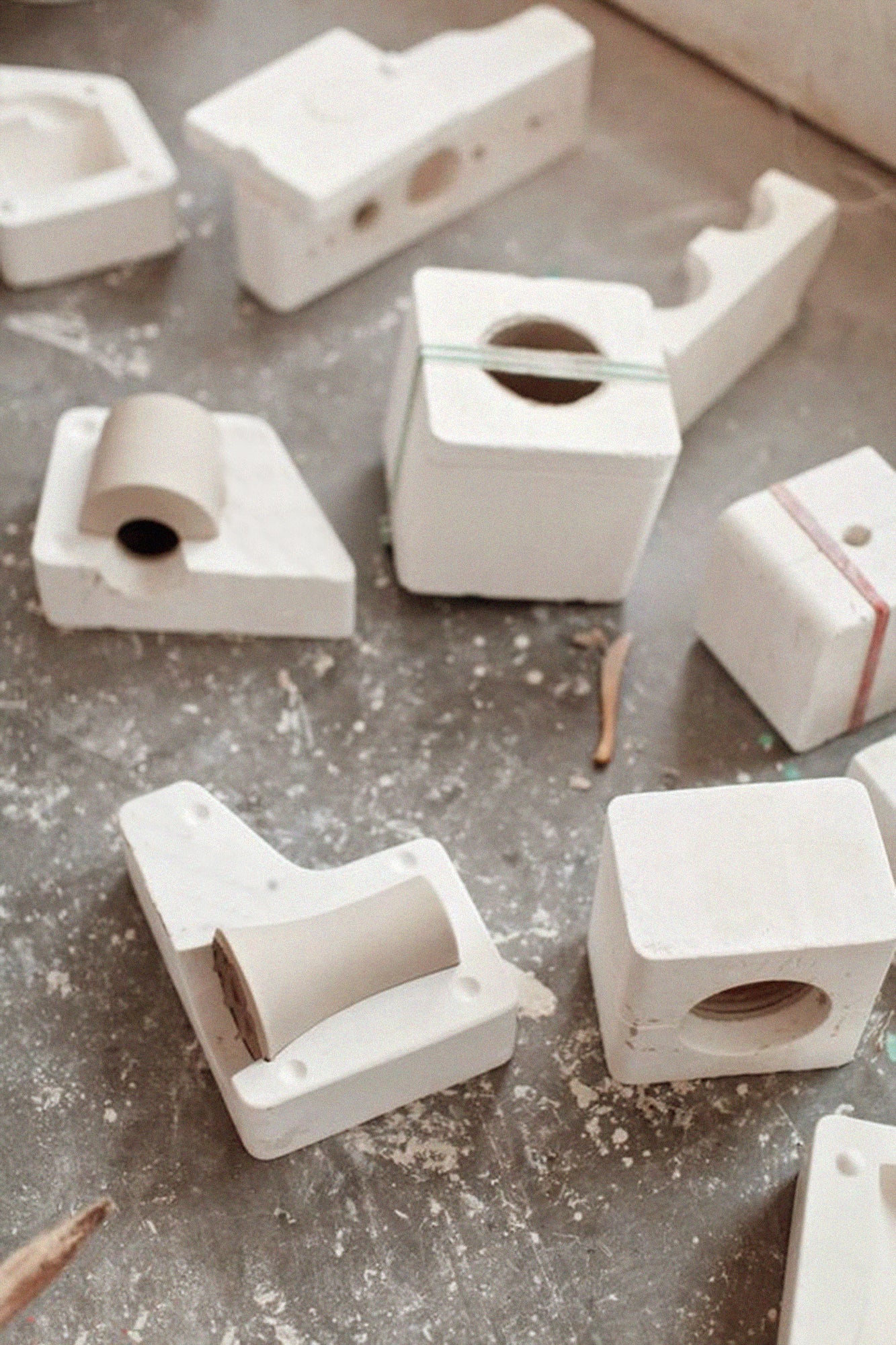
III. Creating the mold
Every mold is the negative of the design to become, the shape. It is made of powder of gypsum from scratch, all by hand, experience, and knowledge. The contraction for porcelain is 14%. The mode will be bigger by 1.4
Composition:
1 l water = 0.7 kg gypsum
Summer - 1/2 weeks to dry
Winter - 3/4 weeks to dry
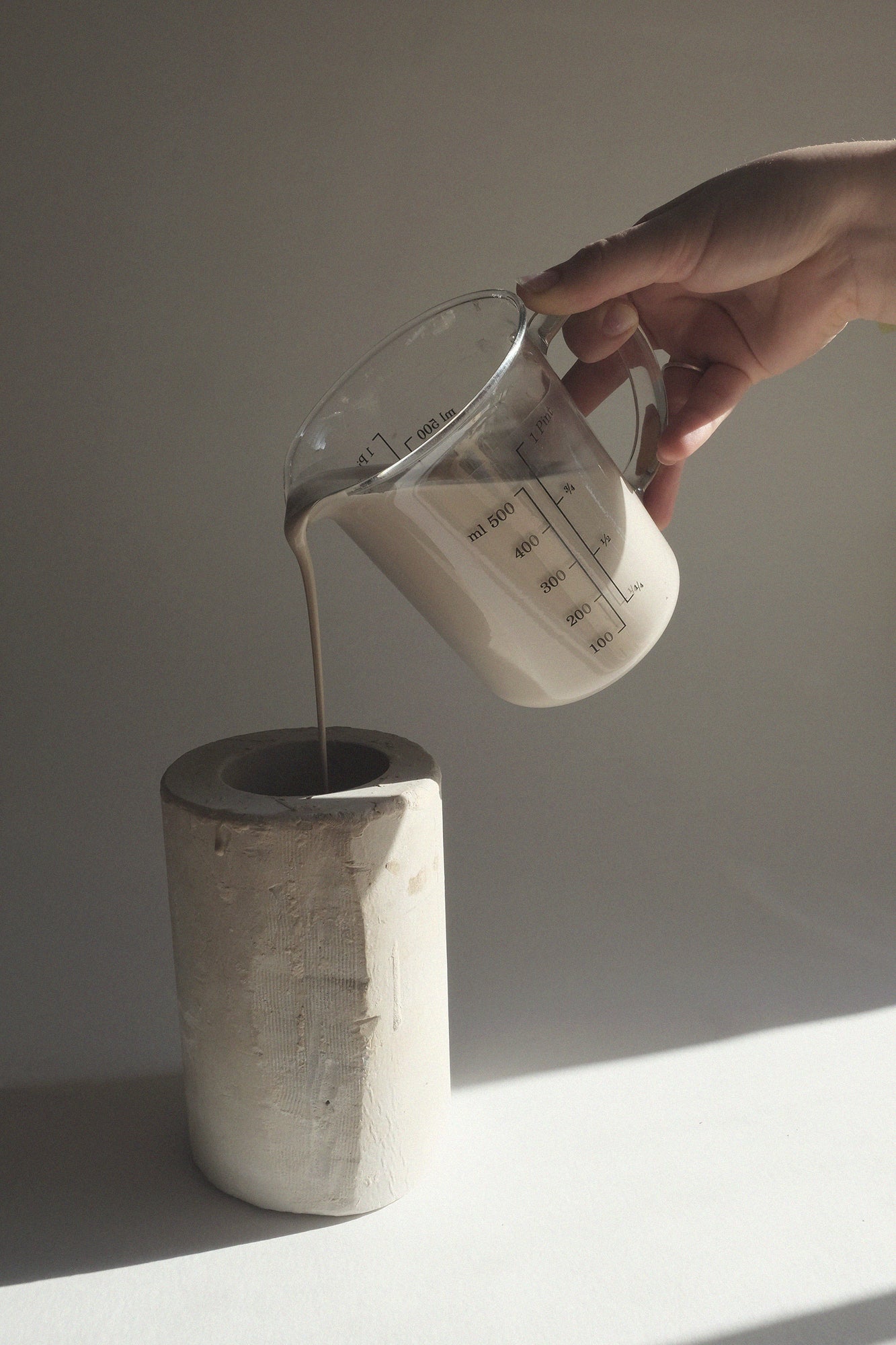
IV. Creating the shell
The porcelain powder, miked with water and hardener becomes liquid milk. Every piece is made by pouring the porcelain mixture into the mold and letting a thin crust to be formed as a result of the absorption of water by gypsum.
5 mins= 5mm thick
10 mins= 7 mm thick
15 mins= 10 mm thick
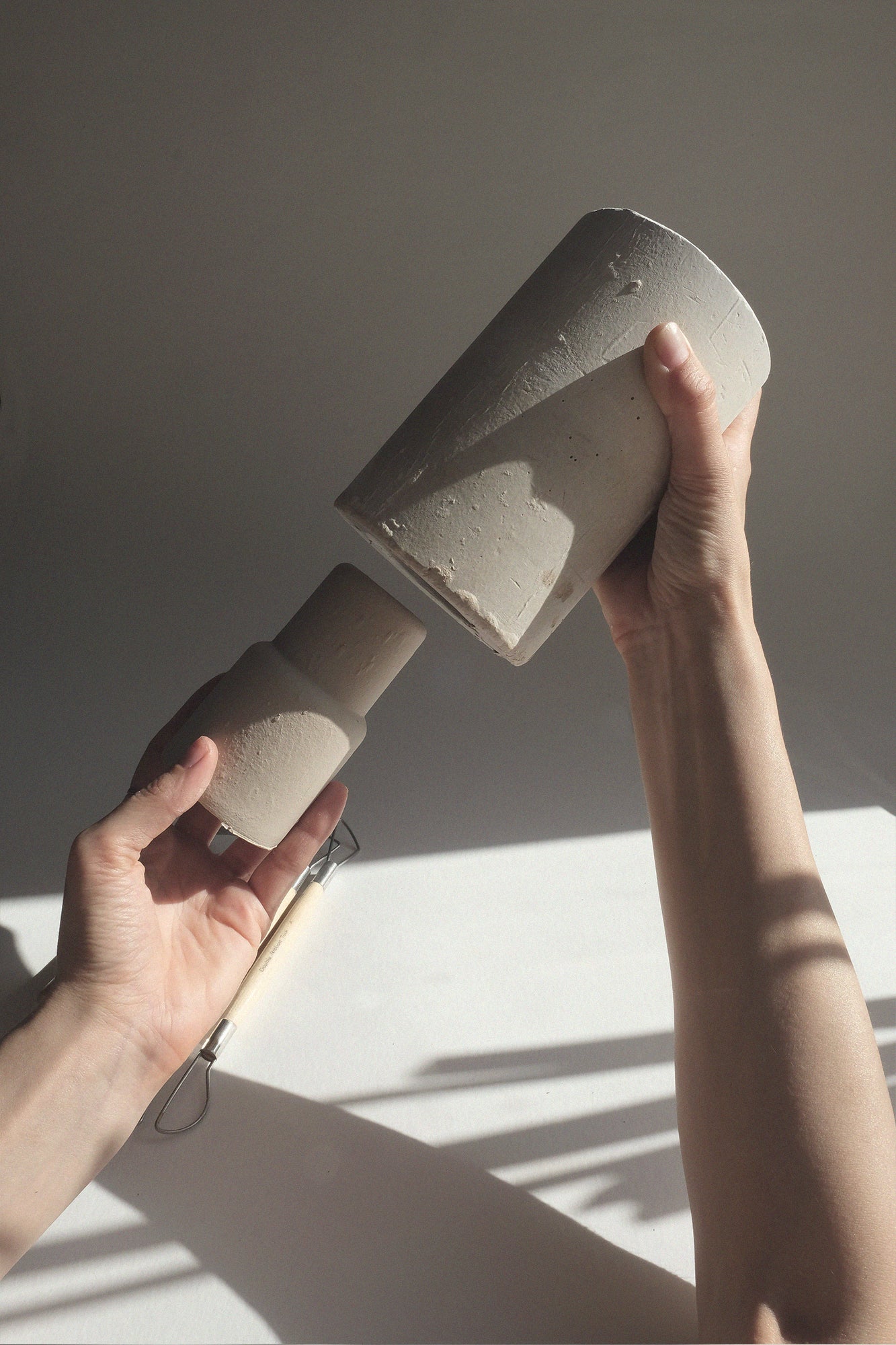
V. The first shape
After taking the piece from the mold, the formed shell is let to dry before first finishing. When it is still wet it is extremely elastic and can be shaped. The material has memory, every change in this stage will reveal itself after the firing. In this stage, it can be transformed, cut, or distorted.
Time to dry - 2-4 days
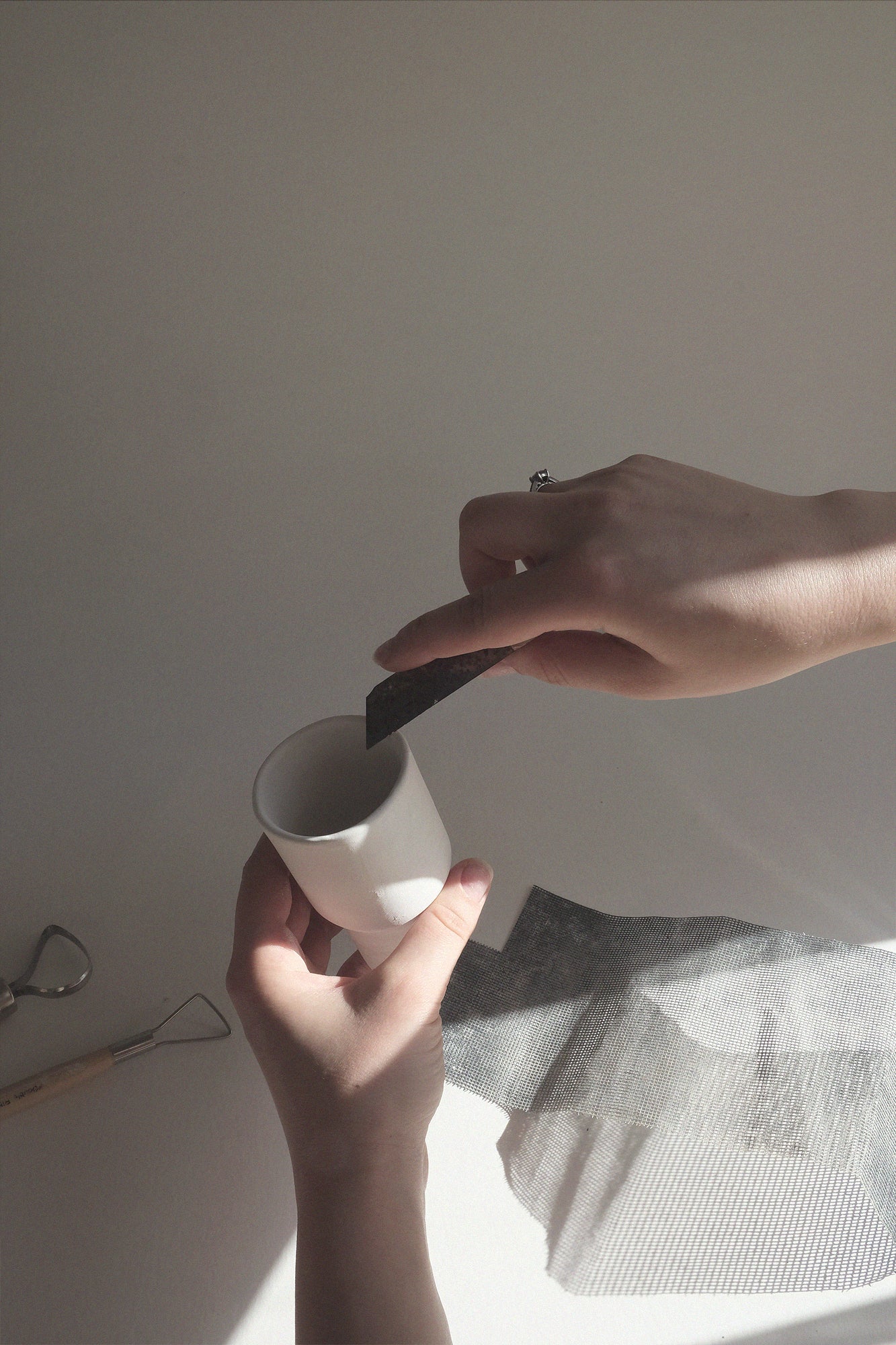
VI. Finishing
The dry shell is finished on top, bottom and surface with a knife and a wet wipe, a mask is required. In this stage all the surface imperfections are reveled. The surface is as fragile as an eggshell. Every wrong move is mortal.
Sandpaper
Knife
Sponge and water
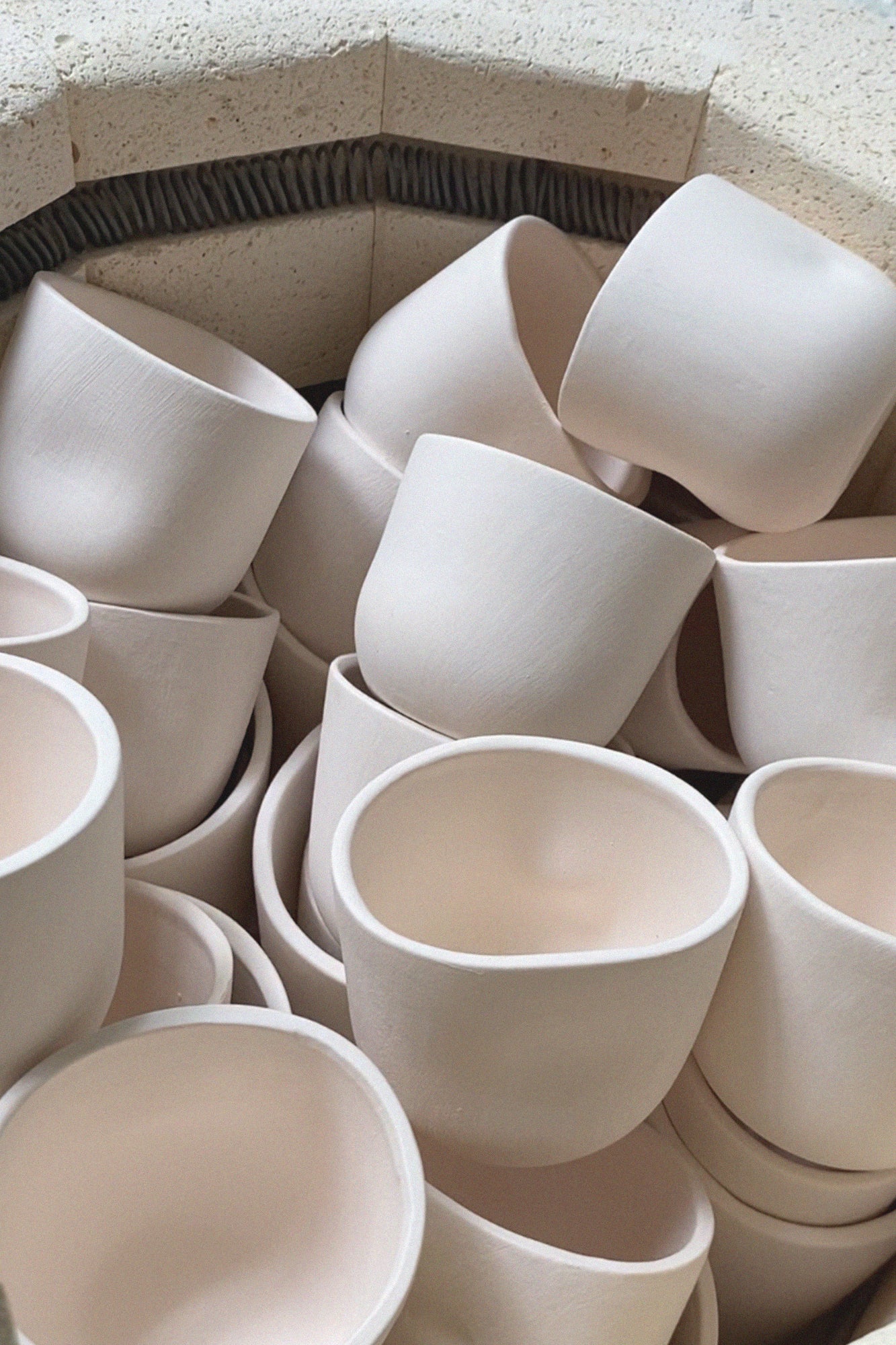
VII. Biscuit firing 900°C
The first burning, at a low temperature of 900°C, is the test of fire. You find out if an object will survive or die. The temperature extracts the water from the object, allowing it to be harder, to draw and glaze it without the risk of melting.
Time in the klin: 60L Klin = 40h
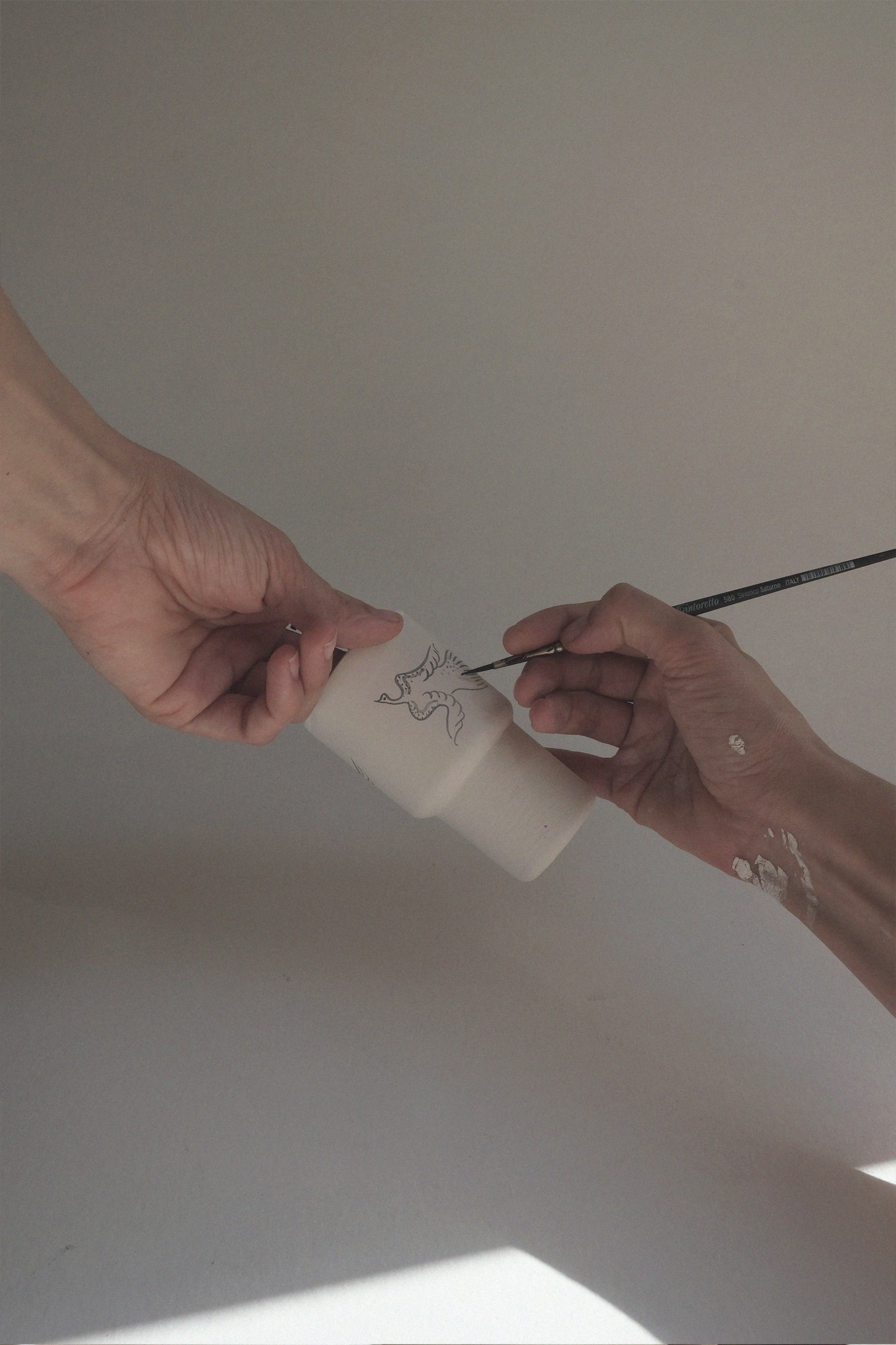
VIII. The painting
The painting is made with cobalt oxide, Co3O4, The most stable pigment. It is made from thermal decomposition of cobalt oxalate nanorods. it reflects the blue of the sky and the transparency of the sea. We are inspired by the timeless motifs of birds, fishes and fairytales symbols.
1g Co3O4 + 5g SiO2 + 10ml H2O
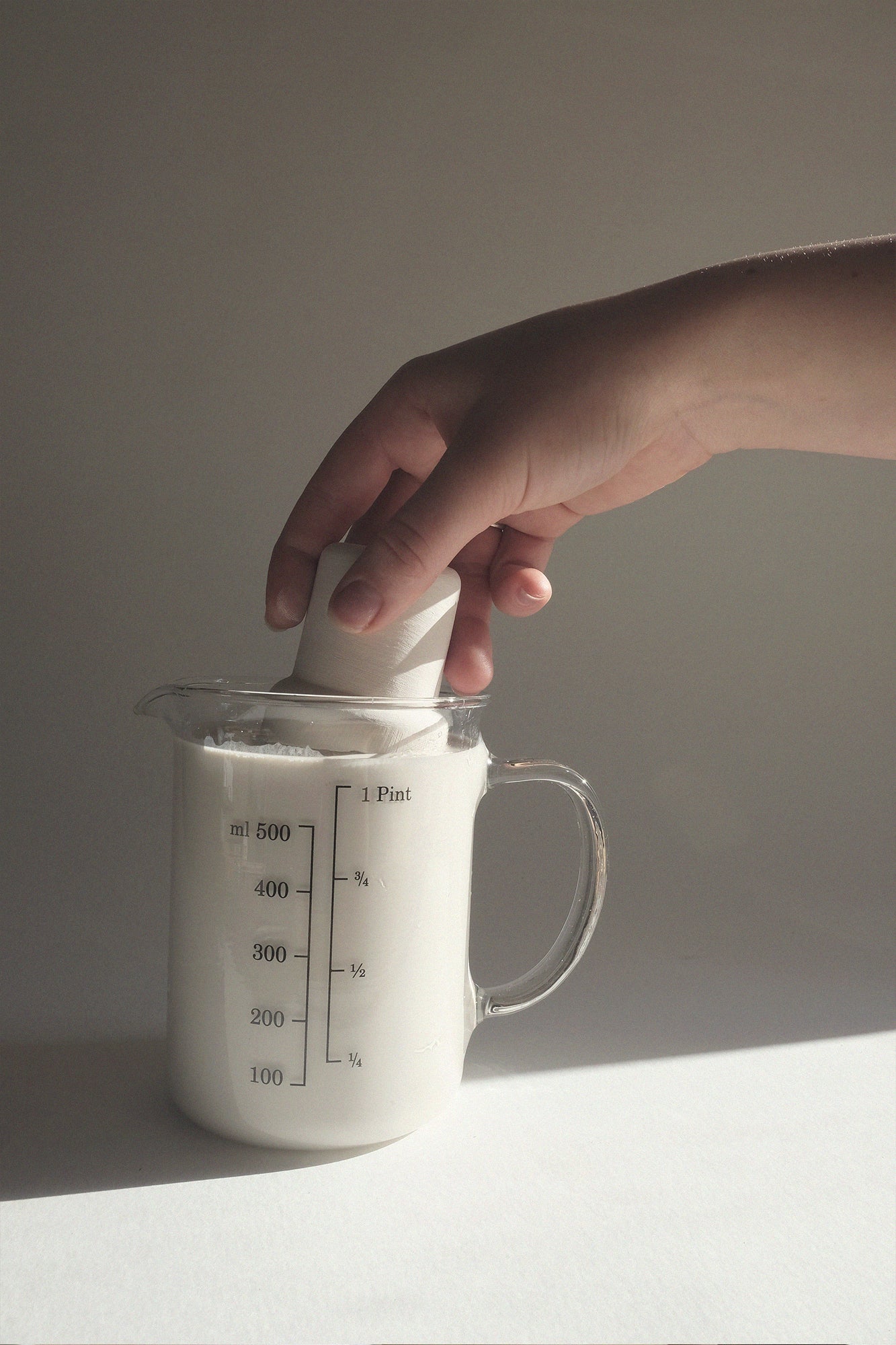
IX. The glazing
The glaze is a layer of liquid silicium, that will melt in the klin and form a protective shiny coat for the object and seal the painting. We make it from the powder of glass by blending it with water. The consistency is close to a fat milk.
Cmposition: 1l water - 350 g glazing SiO2
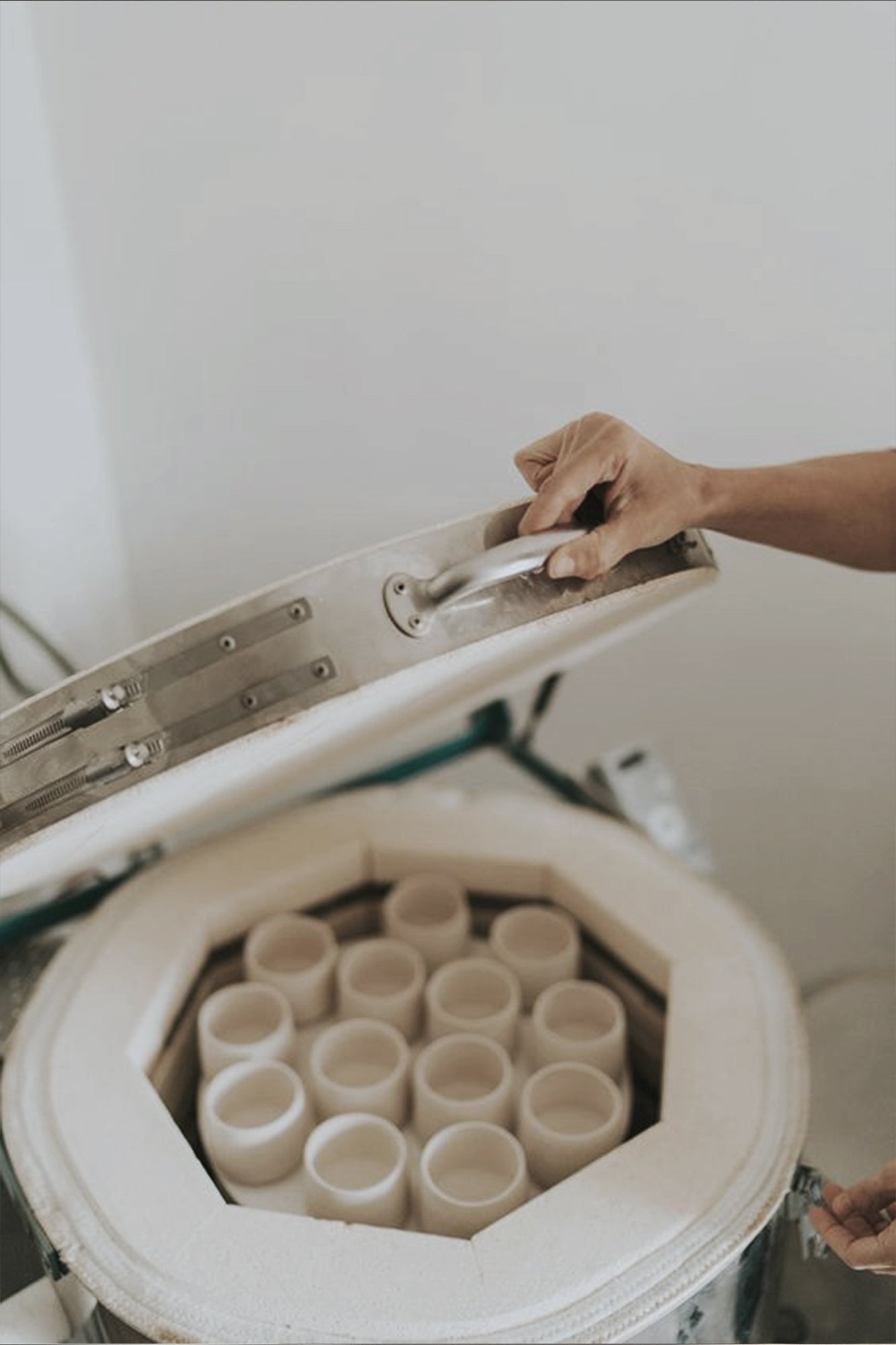
X. Second fire 1230°C
The second firing, at 1230°C results into the funtional object, it is always a surprise the way a object results, the expectations are always different from the reality, this is a lesson that is true for life.
Time of firing: 60 l Klin - 48 h
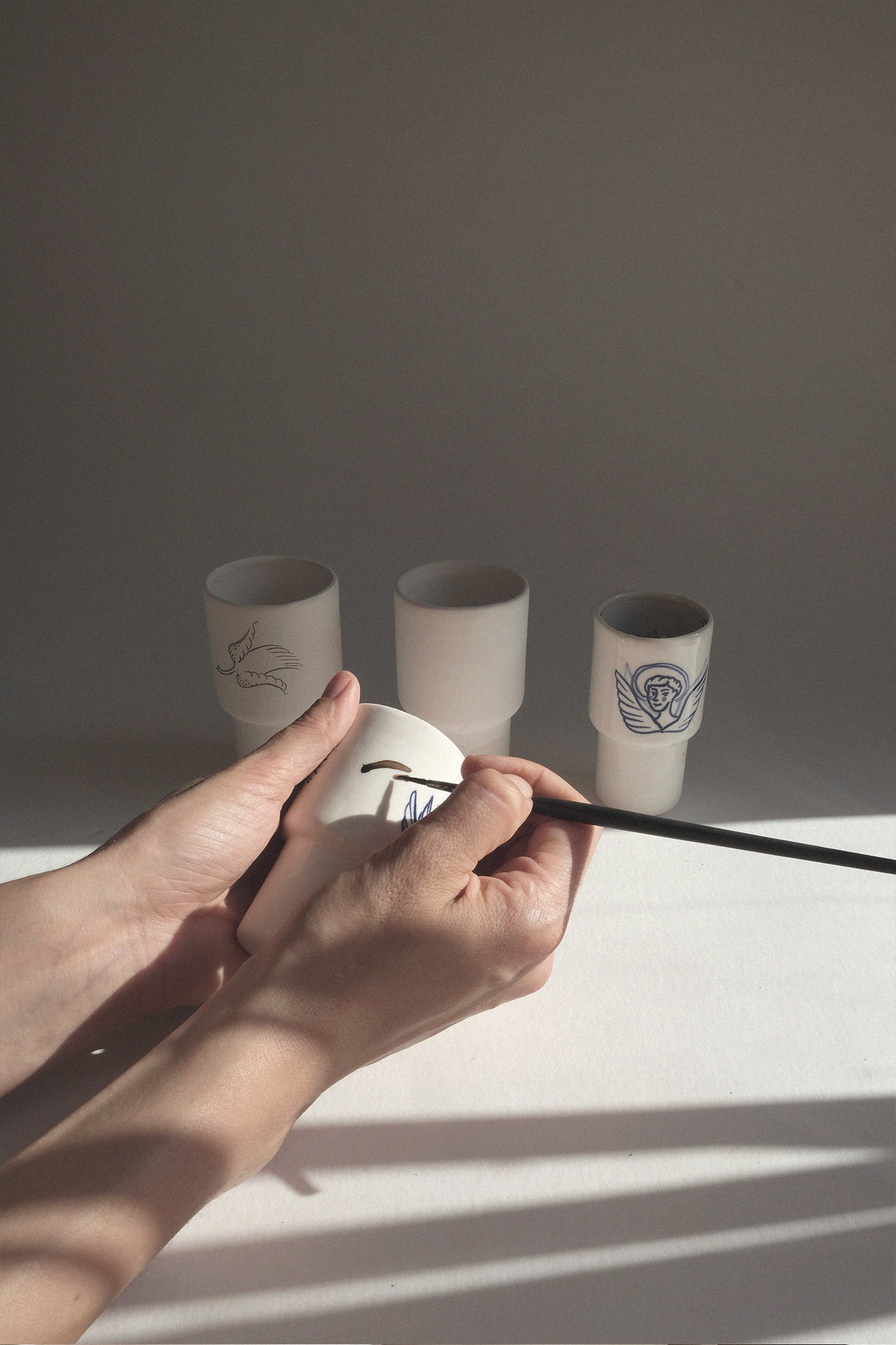
XI. The golden luster
Luster, gold or platinum si a technique for precious objects to give them glitter, accents, or preciosity. We use in only on precious objects that shine from the interior. It necessities a third fire, of 750°C. We use 12% gold or Platinum for the silver.
Overglaze - Au 12%
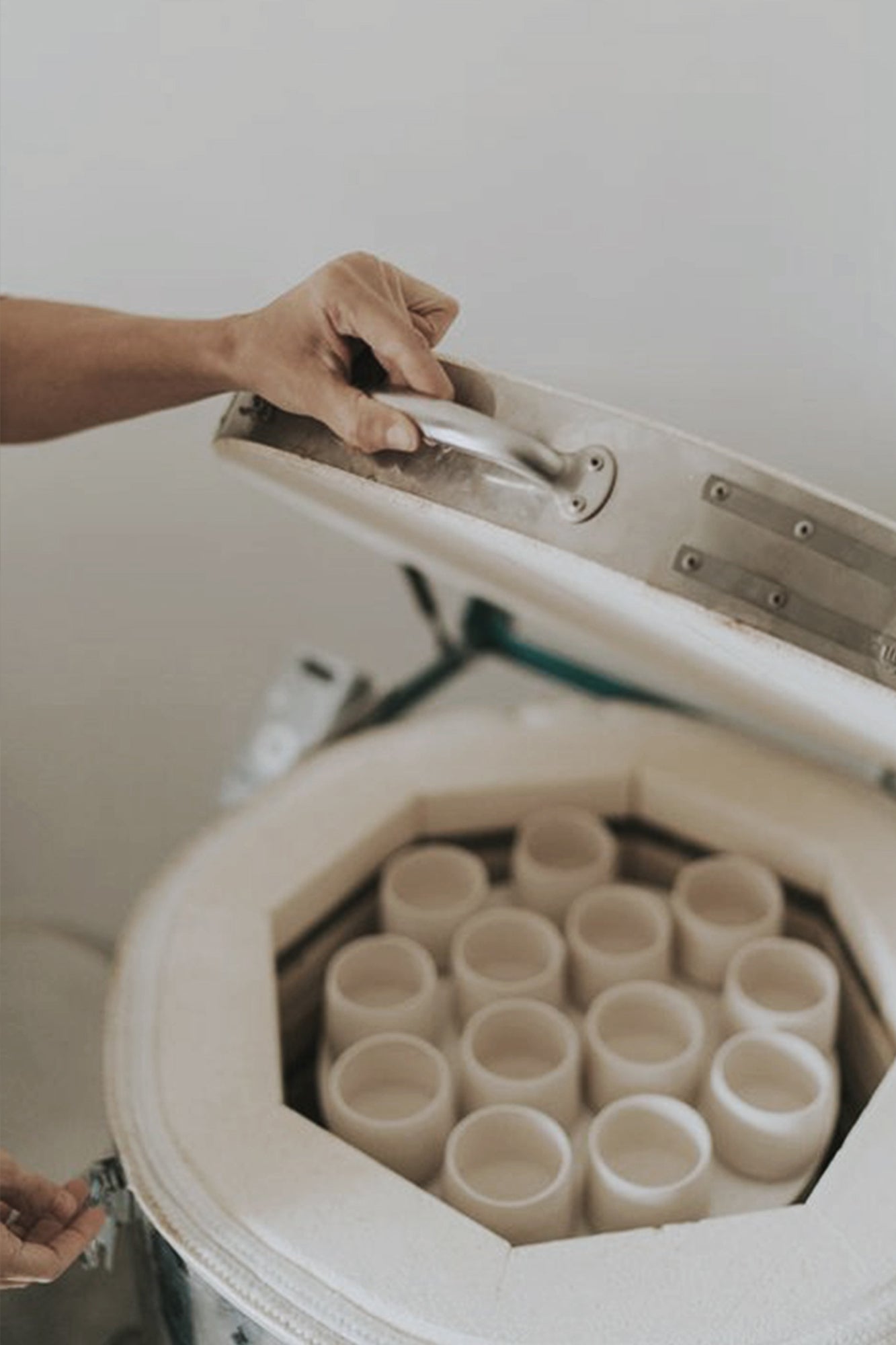
XII. Third fire 750°C
Every object with gold or silver painting needs a third firing to stabilize the luster, this is a low temperature of 750°C. It is called overglaze. You can make it with biscuit firing, at a lower temperature.
Time of firing: 60 l Klin - 38 h
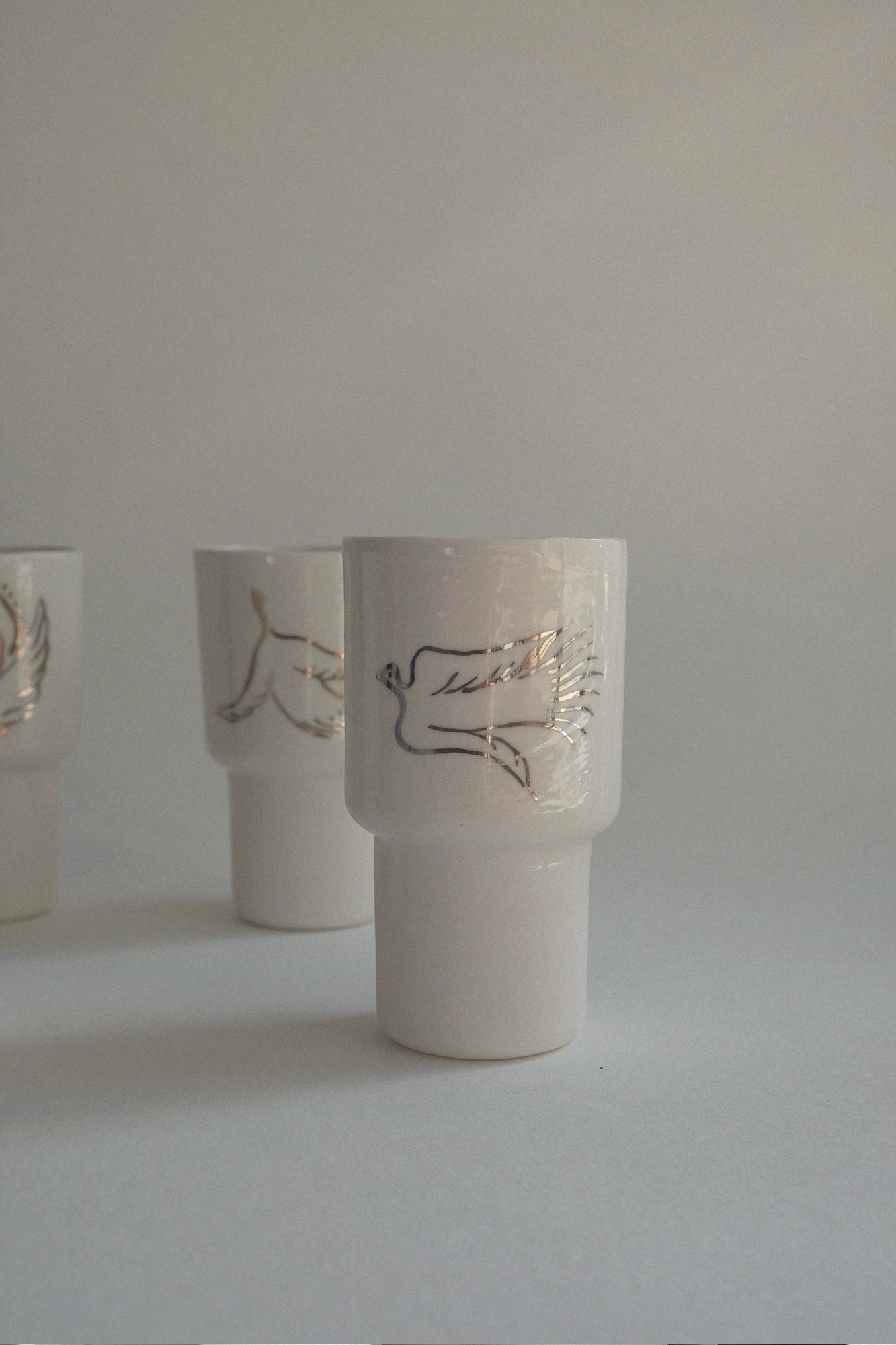
XIII. The object
We are so proud of seeing each object in particular, the way it became, the way it was born on this earth to bring happiness and be special. This is so rare and we appreciate even the broken ones that we gift to the close ones. The closer the friend - the more broken the piece.
From matter to shape
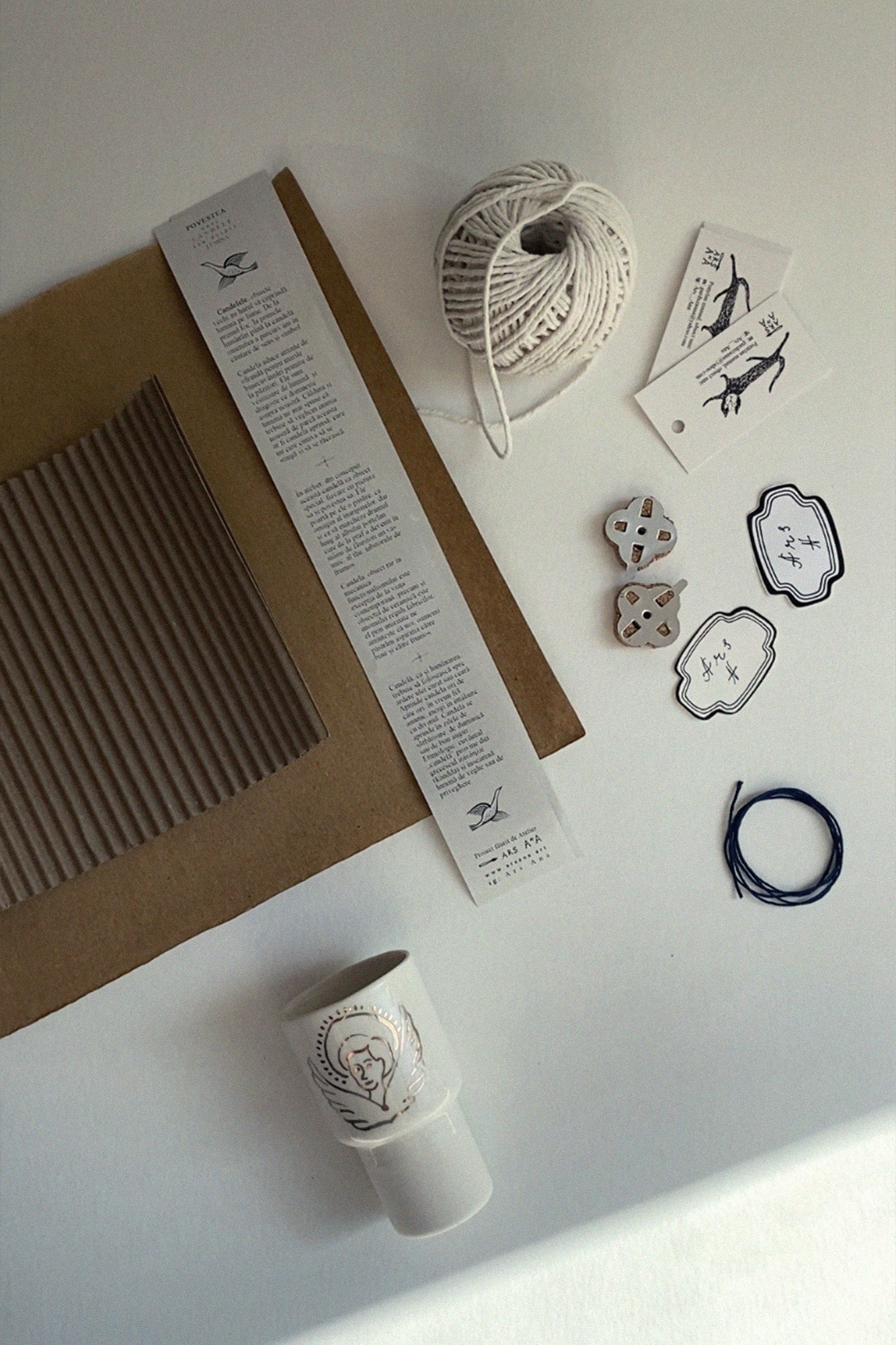
XIV. The packaging
Every object is carefully packaged to become a precious gift, to tell its story of how it was made and the way it was touched, each in part by the hands filed with care and energy. We put time into thinking the colours, type of paper used, sustenability and impact. We use storytelling to transmit the emotion and energy we invested the artefact.

XV. Delivering
We are carefully packing the object to deliver it safely. We are responsible for the way it arrives to bring you joy. The precious object starts a new life in your house, it creates a new story for you and your world. It eventually becomes a portrait of yourself in posterity. We believe in timeless objects that becomes memory.
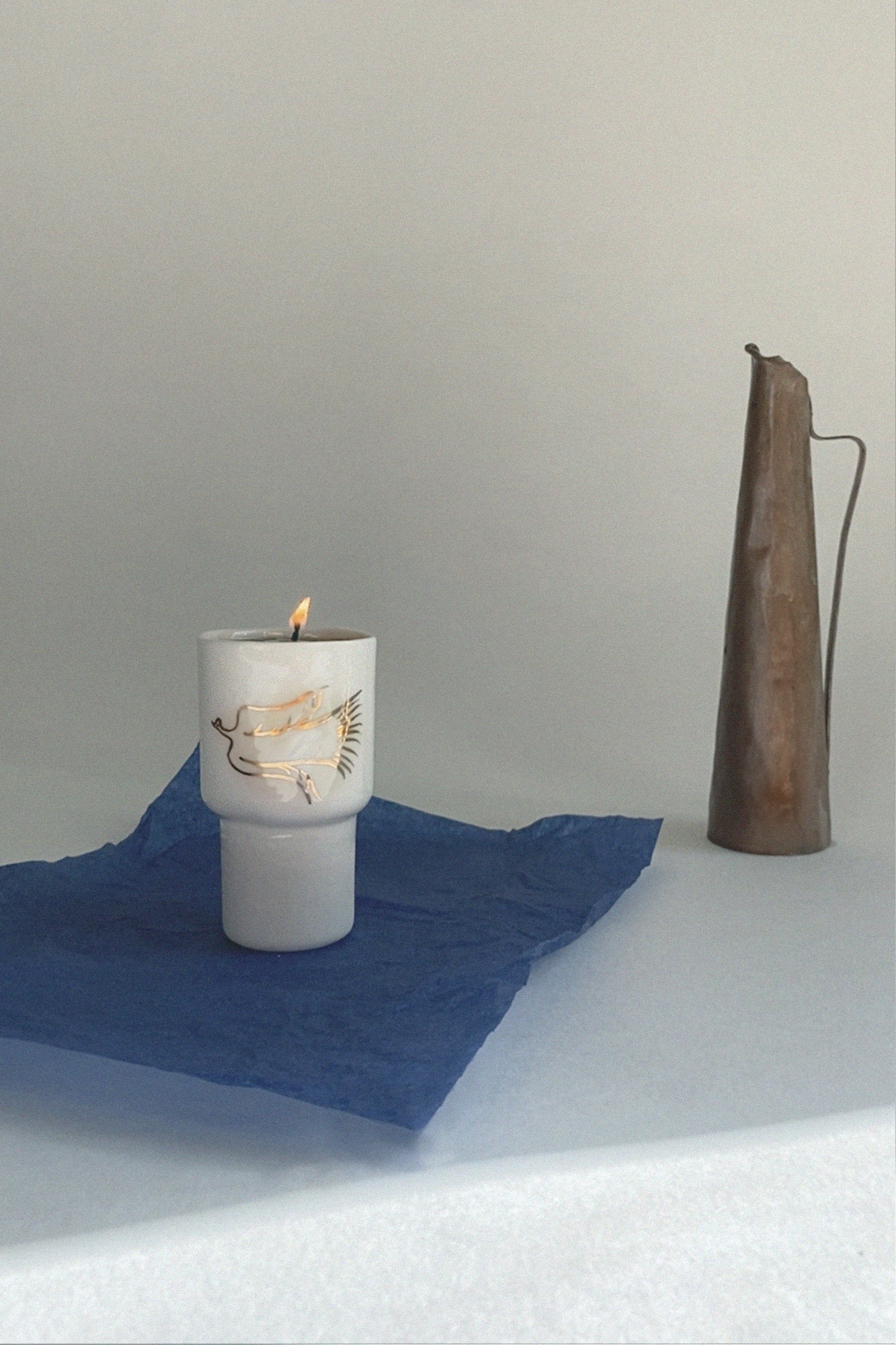
The beauty we share
We believe to reunite the idea with the object, under the material and mental culture. It is meant to bring joy and the aspiration for the invisible, impossible, and imaginary. Come with us, to recreate emotional luxury through unique objects.